The world of acrylic innovation is rapidly transforming, driven by advances in plastic technology and new approaches to design and manufacturing. As we look to the future, the use of acrylic in various industries continues to expand, supported by emerging trends such as 3D printing, sustainable materials, and digital fabrication. In this blog, we’ll explore how these innovations are shaping the future of custom acrylic fabrication and what this means for businesses, designers, and consumers alike.
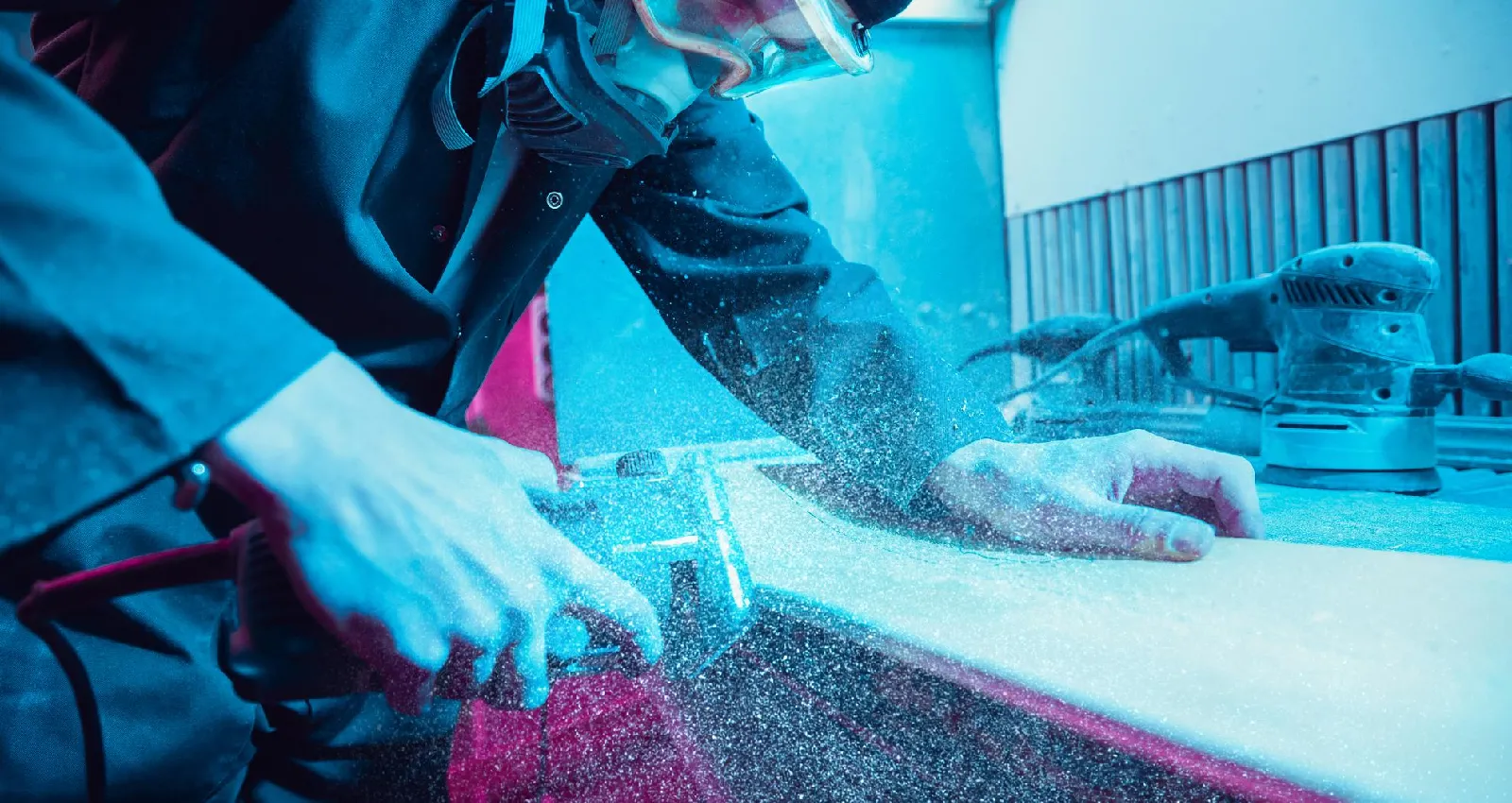
The Rise of Acrylic Innovation
Acrylic, known for its versatility, durability, and optical clarity, has long been a go-to material for industries ranging from interior design to retail displays. But what sets apart the next phase of acrylic innovation is the fusion of traditional techniques with cutting-edge plastic technology. This integration is creating new possibilities for custom fabrication that are more precise, efficient, and sustainable.
A Brief Overview of Acrylic Fabrication’s Evolution
Historically, acrylic fabrication involved manual processes such as cutting, bending, and joining. While these methods are still valuable, the advent of digital fabrication tools and 3D printing has streamlined the production of complex and customized acrylic products. By leveraging these advancements, manufacturers can produce intricate designs with unparalleled accuracy and reduced waste.
The Role of 3D Printing in Acrylic Fabrication
3D printing has revolutionized many aspects of manufacturing, and its impact on custom acrylic fabrication is significant. This technology allows for the creation of complex shapes and structures that were once difficult or impossible to achieve using traditional methods. Here’s how 3D printing is enhancing acrylic fabrication:
Precision and Customization
With 3D printing, manufacturers can achieve intricate geometries that cater to highly specific design needs. This level of precision is crucial for industries like architecture, where custom acrylic components often require unique forms and seamless integration.
Reduced Material Waste
One of the primary benefits of 3D printing is its additive manufacturing process. Instead of cutting shapes from a larger acrylic sheet, which leads to excess material waste, 3D printing builds components layer by layer. This not only minimizes waste but also conserves resources.
Prototyping and Iteration
For designers and engineers, the ability to quickly prototype using 3D printing is invaluable. This technology enables rapid iteration, ensuring that final products meet exact specifications before moving to mass production.
Case Study: Acrylic Prototyping with 3D Printing
Take, for example, a design firm tasked with creating custom light fixtures for a new luxury hotel. Using 3D printing for prototyping allowed the firm to test various shapes and opacity levels of the acrylic sheets, optimizing both the aesthetic and functional aspects. The final products were fabricated with minimal revisions, showcasing how 3D printing enhances design efficiency.
Sustainable Materials in Acrylic Fabrication
As environmental awareness grows, the demand for sustainable materials in fabrication is also increasing. Acrylic, often derived from petroleum-based sources, has traditionally raised concerns about sustainability. However, modern plastic technology is addressing these challenges by incorporating eco-friendly practices.
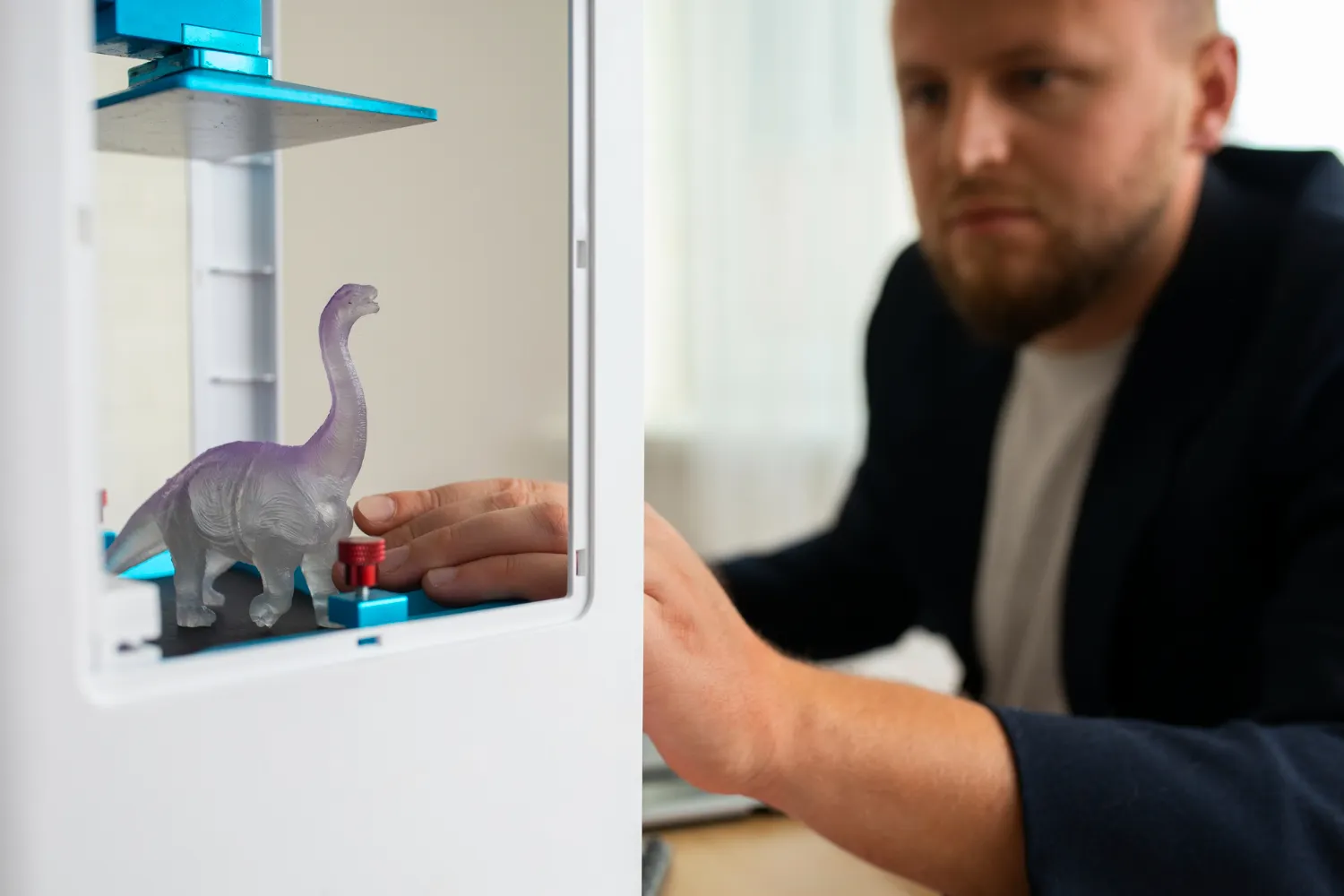
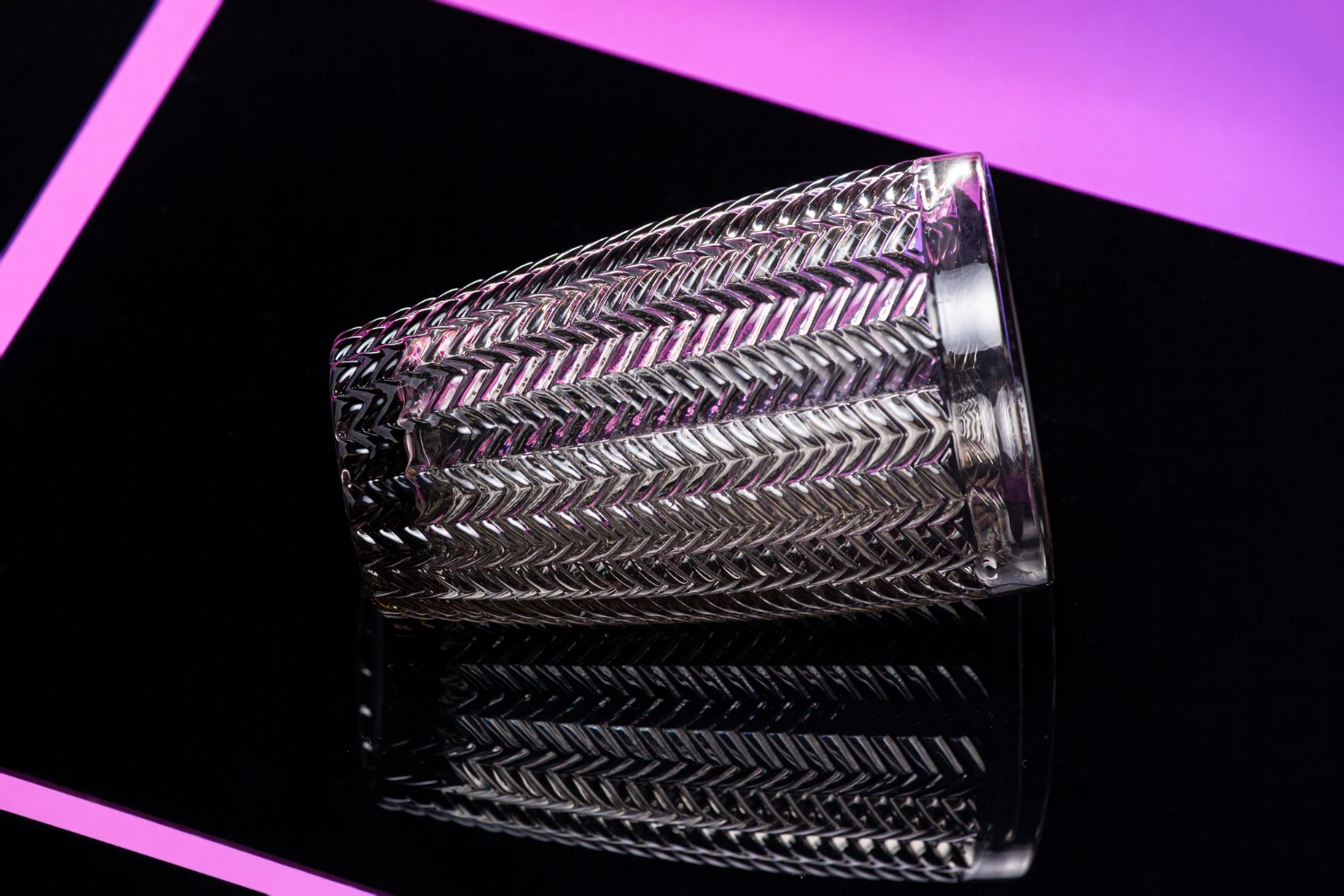
Innovations in Eco-Friendly Acrylic
Recycled Acrylic Sheets
Manufacturers are now producing high-quality acrylic sheets from recycled materials. These sheets offer the same durability and transparency as virgin acrylic but with a significantly lower environmental impact.
Biodegradable Alternatives
Research into bio-based plastics has led to the development of biodegradable acrylic alternatives. These materials break down more readily in natural environments, reducing long-term waste.
Energy-Efficient Production
Advanced manufacturing methods, such as digital fabrication, utilize less energy and produce fewer emissions compared to traditional processes.
The Impact on Custom Acrylic Fabrication
The shift toward sustainable materials in acrylic fabrication not only benefits the environment but also appeals to eco-conscious consumers. Companies that prioritize sustainability are better positioned to attract clients who value ethical and responsible production. For instance, a custom acrylic fabrication company can offer services using recycled or biodegradable materials, reinforcing their commitment to green practices.
The Integration of Digital Fabrication
Digital fabrication encompasses computer-controlled processes such as laser cutting, CNC machining, and 3D printing. The integration of digital fabrication tools into acrylic manufacturing has paved the way for greater precision and versatility.
Benefits of Digital Fabrication for Acrylic Projects
Enhanced Design Capabilities
Digital fabrication allows for the execution of intricate and complex designs that would be challenging to create manually. With advanced software, designers can translate their visions directly into fabrication-ready files.
Streamlined Production
Automated processes reduce human error and speed up production times, making it easier for businesses to meet tight deadlines without sacrificing quality.
Scalability
Digital tools make it simpler to scale from one-off custom pieces to larger production runs. This flexibility is especially important for industries like retail, where display components might need to be produced in varying quantities.
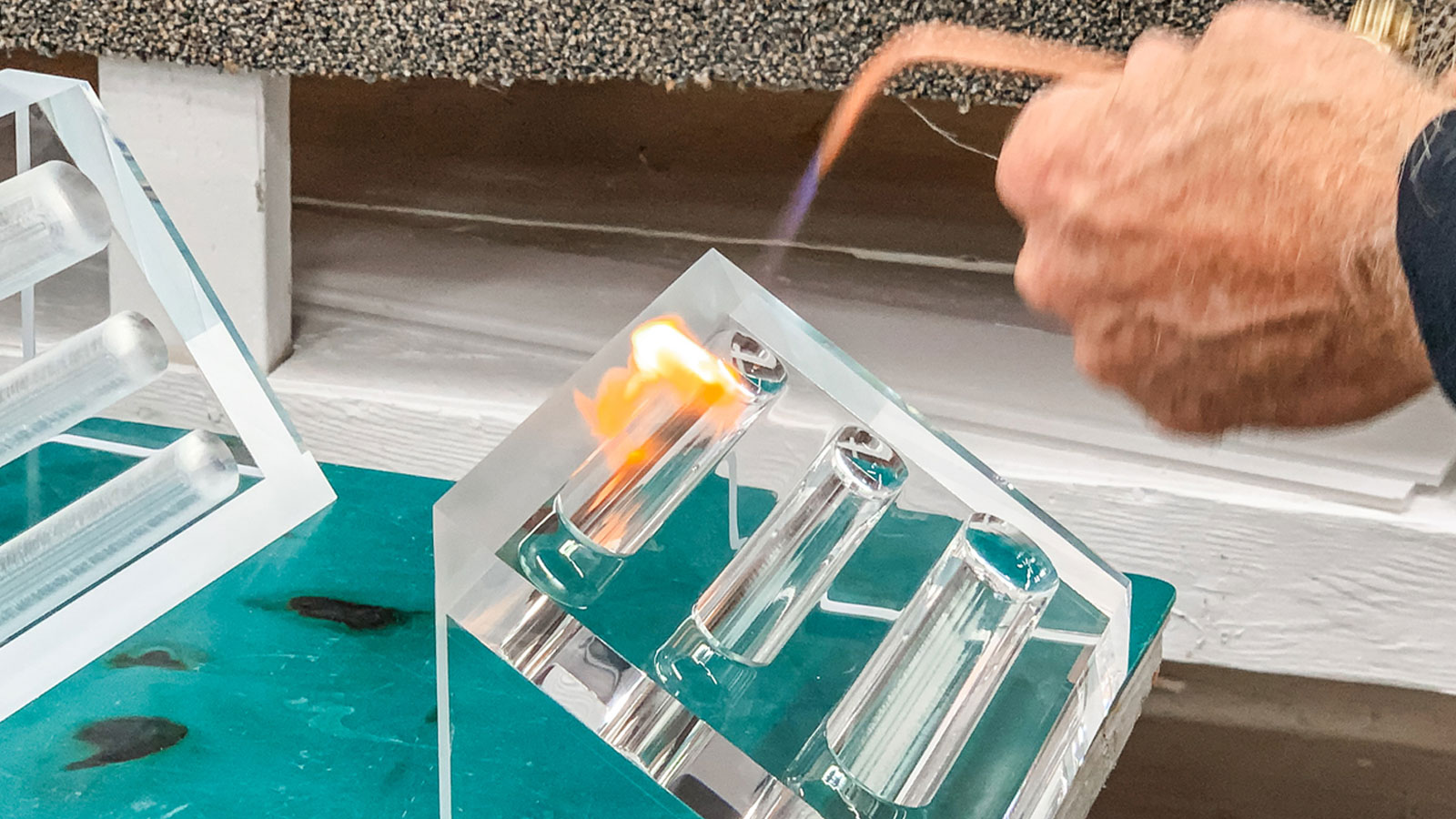
First-Hand Insights on Digital Fabrication
As a seasoned custom acrylic fabrication provider, we’ve embraced digital fabrication techniques to enhance our service offerings. A notable project involved producing a series of high-precision display cases for a museum exhibit. Utilizing digital fabrication tools, we ensured each case was consistent in quality and dimension, meeting the strict criteria of museum curators.
What Lies Ahead for Acrylic Fabrication?
The future of acrylic fabrication is promising, thanks to continued advancements in plastic technology and an ongoing commitment to sustainability. Here are some trends and predictions:
Greater Use of Smart Acrylics
Smart materials, which respond to environmental changes like light or temperature, are making their way into acrylic innovation. Imagine window panels that automatically adjust opacity based on sunlight or decorative acrylic pieces that change color with ambient light.
Expanded Applications in Various Industries
From medical equipment to consumer electronics, acrylic’s versatility will lead to its adoption in new sectors. The use of 3D printing and digital fabrication ensures that acrylic can be adapted to meet the unique demands of these industries.
Collaboration Between Industries
Cross-industry partnerships will foster greater innovation. For example, combining plastic technology expertise with advancements in sectors like architecture or automotive design can lead to new applications and improved functionality.
Conclusion: The Future Is Bright for Acrylic Fabrication
The landscape of custom acrylic fabrication is evolving at an unprecedented pace. With innovations in plastic technology, the adoption of 3D printing, and the push for sustainable materials, the future holds endless possibilities. For those looking to embrace acrylic innovation, now is the time to invest in these technologies and practices. By staying ahead of trends and incorporating advanced digital fabrication methods, companies can lead the charge in redefining what’s possible in acrylic manufacturing.
FAQs
What is acrylic innovation?
Acrylic innovation refers to the advancements in manufacturing, design, and use of acrylic materials, often incorporating modern plastic technology to improve quality, functionality, and sustainability.
How does 3D printing benefit custom acrylic fabrication?
3D printing enhances custom acrylic fabrication by allowing for precise, complex designs, reducing material waste, and speeding up the prototyping process.
Are there sustainable options in acrylic fabrication?
Yes, manufacturers are now using recycled acrylic sheets and developing biodegradable alternatives, aligning with the growing trend toward sustainable materials.